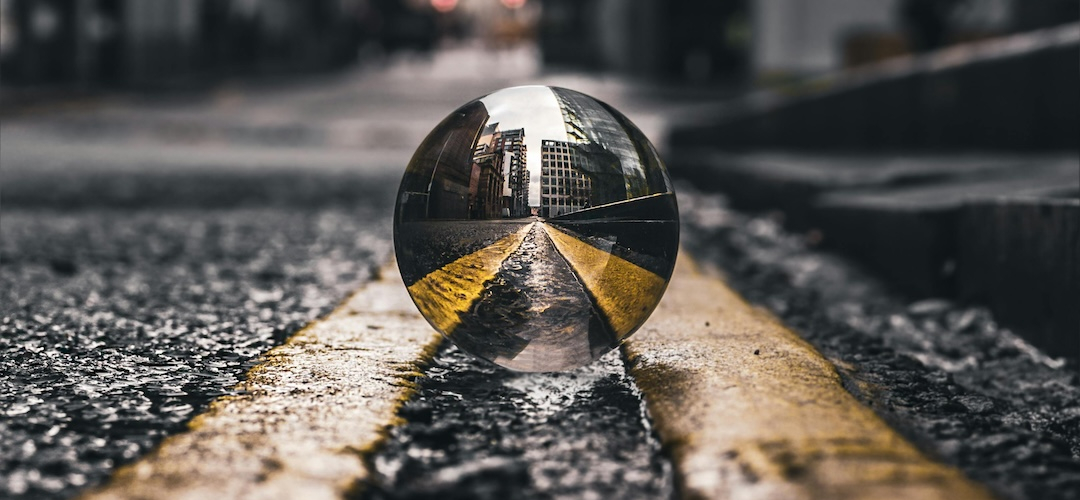
Understanding Predictive Maintenance
What if you knew what maintenance was actually needed instead of guessing? Predictive maintenance is an approach that leverages data, analytics, and technology to predict when equipment or machinery is likely to fail. The benefit of that is that it allows for faster, more efficient maintenance and repairs. This helps to minimize organization downtime, reduce maintenance costs, and optimize the lifespan and performance of assets.
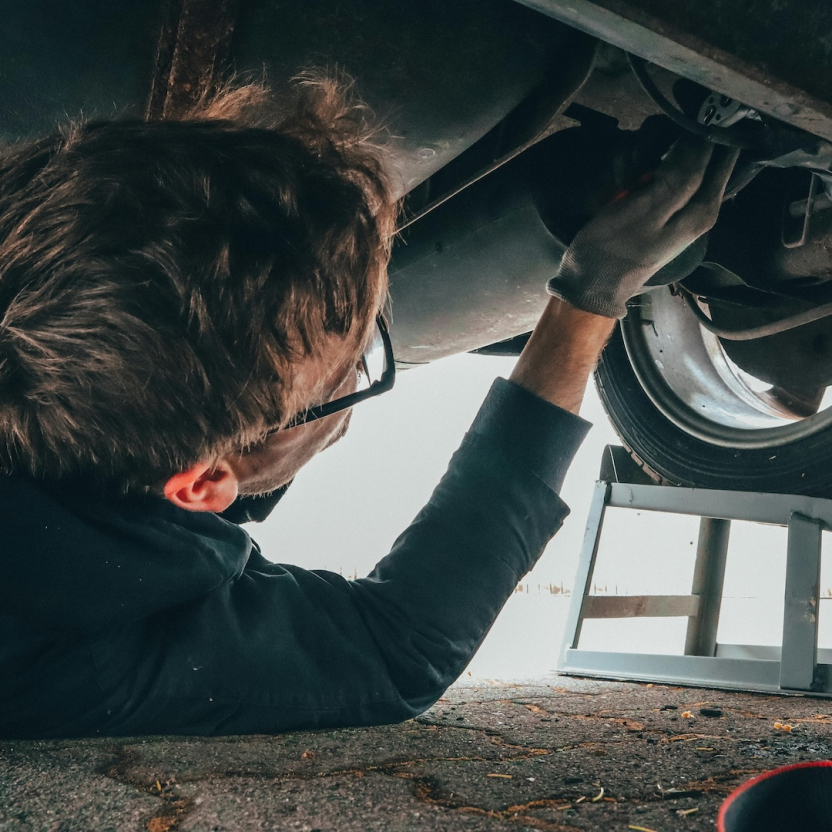
What Are the Key Concepts Behind Predictive Maintenance?
Predictive maintenance can do a great deal for your organization. Key concepts include:
Data Collection: It works to continuously monitor and collect data from sensors, meters, and other monitoring devices attached to equipment. This data can include information about temperature, vibration, pressure, fluid levels, and other relevant parameters.
Data Analysis: Once the data is collected, advanced analytics and machine learning algorithms are applied. From this point, the system works to identify patterns, trends, and anomalies. By analyzing historical data, the system learns the normal operating behavior of equipment. This helps ensure better accuracy.
Anomaly Detection: When something is off, the system knows it. Predictive maintenance systems can detect deviations from normal operating conditions. Unusual patterns or changes in equipment behavior may indicate potential issues or impending failures.
Condition Monitoring: Real-time monitoring of the condition of equipment helps assess its health and lets maintenance teams intervene when the equipment’s condition indicates that maintenance is necessary. That means it is not an automatic, fixed period where the vehicle may not need maintenance.
Predictive Algorithms: Predictive maintenance uses algorithms to predict the remaining useful life of components or systems. By forecasting when a failure is likely to occur, maintenance activities can be planned and executed just in time, minimizing downtime and unnecessary maintenance.
Maintenance Planning: Now that it has these predictions, ordering parts, allocating other resources, and coordinating tasks more efficiently is possible.
Cost Reduction: Predictive maintenance aims to reduce overall maintenance costs as a direct result. It does this by ensuring the necessary maintenance is done but not the unnecessary steps.
Asset Optimization: By addressing issues before they lead to failure, predictive maintenance extends the lifespan of equipment and improves its overall reliability and performance. In industries where there is downtime risk, such as risks impacting production, manufacturing, transportation, and energy, this resolves those concerns.

Data Drives Predictive Maintenance
Collecting vehicle data for predictive maintenance involves monitoring the condition and performance of the vehicle. Here are some common methods used to collect vehicle data for predictive maintenance:
Mobile Data Capture: Drivers and technicians can use mobile data capture solutions to collect analog information on and related to a vehicle, like license plates, odometers, vehicle identification numbers, IDs, tire size, make, model, and tread depth. This is particularly important for fleet operators and service centers as they must accurately match vehicles with the right owners or drivers and any historical data they may have collected on that vehicle.
On-Board Diagnostics (OBD) Ports: OBD-II ports are standard in most modern vehicles. OBD-II devices can be connected to these ports to collect real-time data on engine performance, fuel efficiency, and other essential parameters.
Telematics Devices: Telematics devices are installed in the vehicle, often utilizing the OBD-II port. These devices can collect and transmit data wirelessly, providing information on location, speed, engine health, and driving behavior.
Sensors: Various sensors can be installed in different parts of the vehicle to monitor specific parameters. For example, sensors can measure tire pressure, temperature, vibration, brake wear, and fluid levels.
GPS Systems: Global Positioning System (GPS) technology can be used to track a vehicle’s location and movement.
Fleet Management Software: Fleet management systems provide a centralized platform for monitoring and analyzing vehicle data. These systems integrate with telematics devices and may offer features such as route optimization, maintenance scheduling, and fuel management.
Connected Vehicles: Modern vehicles equipped with connectivity features can transmit data over the internet. This includes data on engine diagnostics, performance, and other relevant parameters.
Smartphone Apps: Apps installed on drivers’ smartphones can collect driving behavior, location, and vehicle performance data. Some apps connect to the vehicle’s OBD-II port via Bluetooth for additional data.
IoT Devices: Internet of Things (IoT) devices can be integrated into the vehicle to collect data on various parameters. These devices may communicate wirelessly to a central system for analysis.
Fleet Tracking Systems: Fleet tracking systems use GPS and cellular technology to monitor the location and movement of vehicles. These systems often provide real-time data on vehicle status and performance.
Automated Diagnostic Systems: Some vehicles come equipped with advanced diagnostic systems that continuously monitor the health of the vehicle’s components. These systems can detect issues and provide alerts for predictive maintenance.
Once the data is collected, it is usually transmitted to a central server or cloud-based platform where advanced analytics and machine learning algorithms can analyze the information to predict potential failures and recommend maintenance actions.
Key Take Aways
The bottom line is that the use of predictive maintenance – through all of these connected tools, sensors, and resources – allows companies to save money and time. It ensures work is done when needed, not just on schedule, and minimizes the risk of downtime.