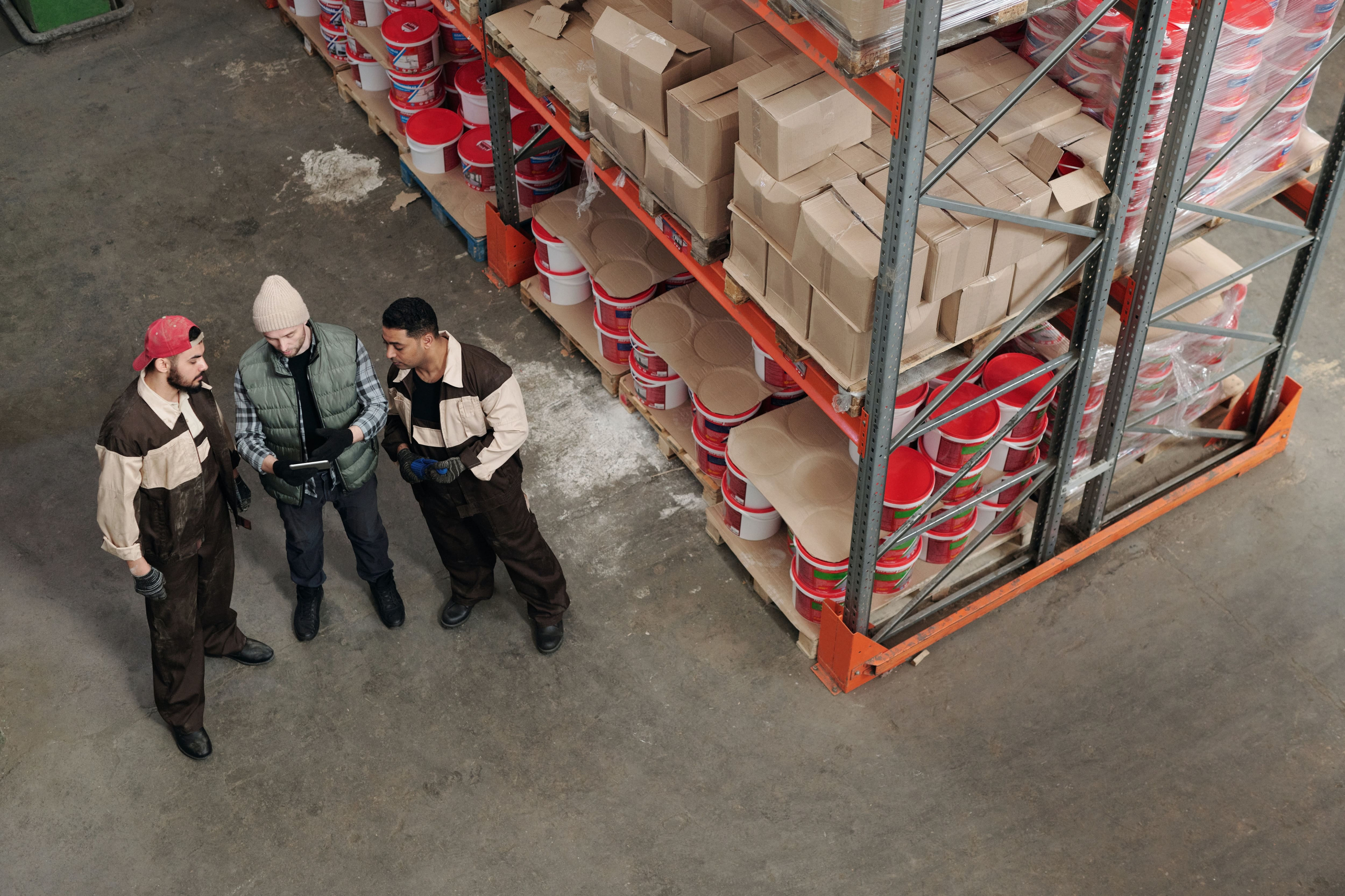
How to Use a Smartphone Barcode Scanner for Inventory Management
Modernizing, streamlining, and upgrading inventory management systems makes sense for most companies. Yet, the process doesn’t have to be complex or even overly costly. Barcodes are perhaps the most effective and efficient method for doing so. Let’s take a look at how barcodes aid in inventory management and how easy it can be to put in place a barcode inventory management system within your own organization.
Barcode Inventory Control Gives You Clear Benefits
Barcode inventory control systems offer numerous benefits including speeding up the shipping and receiving of goods process. They also ensure a more accurate count of materials and products. The system is easy to implement – a matter of just printing and placing barcodes that are later scanned throughout every step of the inventory control process. It allows for complete tracking of everything on the warehouse or stockroom floor, but also provides a fast way of tracking that material. This reduces labor costs, too. Even organizations with large databases of products easily know where a single item is at any given time.
Setting Up a Barcode Inventory System
The system enables the efficient creation of barcode identifiers as products arrive at the location. These are then affixed to the products themselves. They can then be scanned through the point-of-sale (POS) system as sold or returned. The entire time inventory figures can then be accurately managed.
To put this system in place, you’ll first:
- Identify the kind of barcodes you will use based on industry and application – there are numerous types of barcodes supported, with UPC and SKU as two of the most common.
- Decide what their function will be such as capturing data as products come in.
- Decide what information they will carry. For example, a one-dimensional barcode can store less than 100 characters, but two-dimensional upgrade this to up to 1500 characters.
- Choose the type of device used, such as dedicated devices or scanning guns, or, which is most common today, the use of smartphones or ruggedized devices.
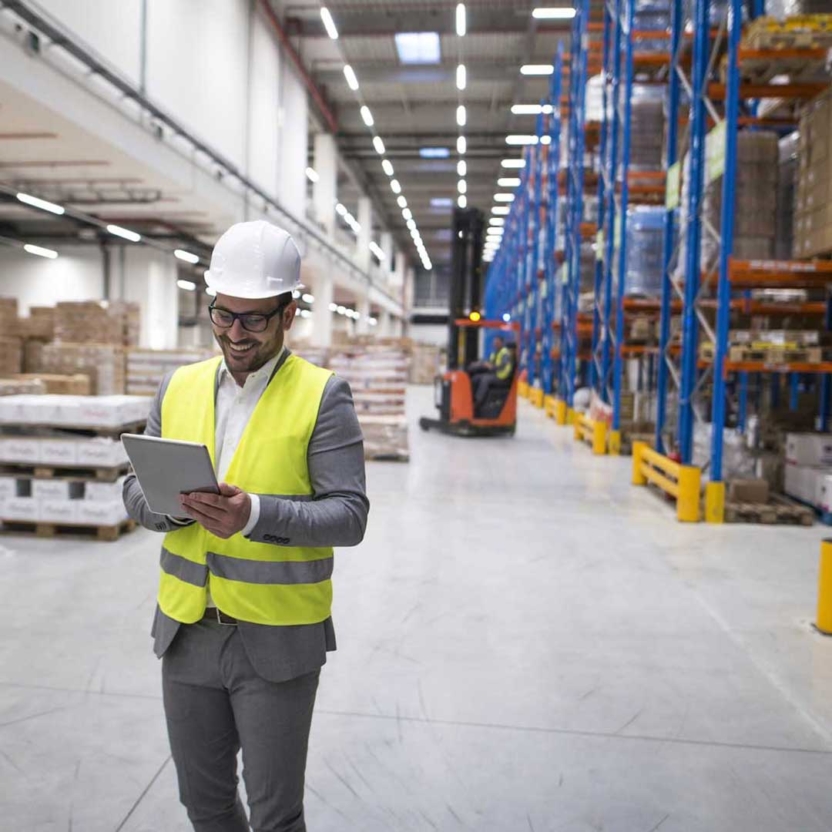
UPC and SKU? Which One Matters Most?
The Universal Product Code (UPC) and Stock Keeping Unit (SKU) are terms commonly used in inventory control for retail establishments. While both are barcodes, UPCs are coordinated through GS1, a centralized organization of manufacturers and vendors. This makes it easier to research and compare product pricing as no company can use UPC for their product outside of this, protecting the product’s brand.
SKU is different. It’s used as an internal control for companies allowing organizations to monitor stock through the ownership process – from being received to being sold. Companies never register these barcodes with any organization. Rather, the internal SKUs are flexible to be used as they see fit.
Barcodes May Not Always Be Ideal
In some situations, barcodes do not provide the right avenue for inventory management. There are times they can be damaged during normal wear and tear, making it impossible to function. In these cases, the product serial code can be used as a way to capture that data. To ensure your team can capture the data they need in any situation, consider integrating both barcode scanning and optical character recognition together so that your workforce can record and digitize serials numbers whenever required.