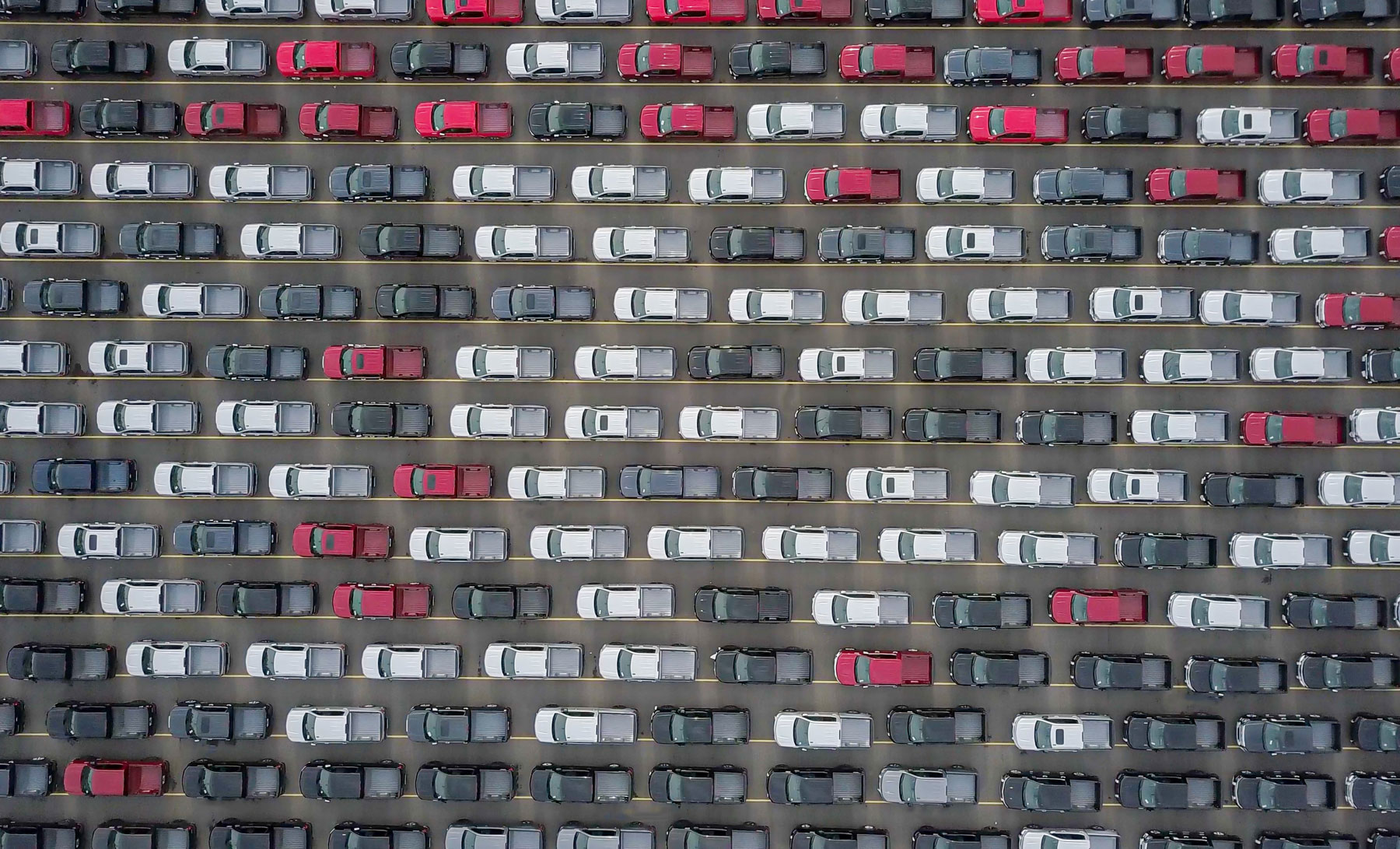
How Mobile Data Capture Improves Tire Maintenance for Car Fleets
The humble tire does a lot more than get you from A to B. It should give you great performance, absorb every bump and shock, and keep you safe on the road.
For car fleets, tires work especially hard, and need more frequent maintenance. From general wear and tear to the air pressure, and tread depth, it takes some work to keep them operating at their best. But it sure pays off. Proper tire maintenance not only increases vehicle safety but can also improve fuel economy and extend tire life by 4,700 miles. The key to high performing, well-maintained tires is effective tracking.
Jump to key topics
Jump to key topics
Why do fleets need to keep track of their tires?
Fleet managers know that visibility is integral when it comes to their cars. They need to know what state the vehicles are in, how many miles they have gone and when their last inspections took place.
The same is true of the tires on each vehicle. Having up-to-date inventory records on each tire means that managers know when replacements are needed so that their vehicles are not suffering performance losses by running on old tires. As a general rule of thumb, most manufacturers recommend replacing tires that are 10 or more years old. Tires that are 5 to 6 years old need annual inspections to ensure their safety.
But tire traceability is even more important for responding to product recalls. When a tire is recalled by its manufacturer, it should immediately be replaced and no longer considered safe to drive. This is a significant responsibility for fleet managers, who need to have a system in place to properly record the age, type of each tire, along with the vehicle it is currently on.
What needs to be done to track them?
Tracking a tire is more difficult than other products as it does not have a barcode. However, each tire does have codes on the sidewall that can be used to track them and help manage tires in a car fleet. These are registered to a database with proper identification for each tire.
Every tire has a TIN – tire identification number, which is also known as a tire DOT code, as this number is certified by the Department of Transportation in the United States. This code contains the date of production for the tire, the batch number (a unique ID number in fleets), and an ID number in case of product recall.
This information can be collected and paired with vehicle information so that it is easy to trace which tires are on what car. For the vehicles, fleet managers can record the license plate or the vehicle identification number, or VIN.
These two components enable proper tracking of tires based on their age as well as their use. This data is valuable to fleet managers when it comes to tracking individual tires with ease.
How is it a challenge for car fleets?
Not every car fleet is the same. Some may have a few dozen vehicles, others a few thousands! And when you’re tracking tires, you have to multiply this number by 4 to keep track of them all.
Inevitably, it takes a long time for technicians to record the TIN numbers and VIN for each vehicle. It’s a tough job – and a hotbed for human error. Reading up to 17 black numbers on a black surface often leads to mistakes when recording this data.
If problems occur in this process and they are not registered properly, it’s impossible to know where each tire stands. In the case of a recall, this creates a safety hazard present that’s not easy to overcome.
What technologies can help?
Optical character recognition (OCR) offers a comprehensive solution to this problem. By integrating mobile scanning into your fleet management app or website, your workforce can scan tire DOT codes, VIN numbers and license plates – all with any standard smartphone.
In this way, technicians can automate the process of data entry, and complete the tedious and time consuming process for each tire in a matter of seconds. This is far more accurate than writing or typing numbers into the system. It is also easier to do with a handheld mobile device or phone.
When integrated into your process, mobile OCR scanning makes tracking tires as easy as taking a photo with a smartphone. At the same time, it gives technicians back precious time that they can spend performing their core activities.
Anyline OCR technology even works offline and in adverse conditions. It integrates into existing applications and makes management easy. That means there’s better management of labor with comprehensive tire logging based on key data.
Conclusion
When it comes to fleet management, it takes a lot of work to keep every vehicle well maintained and at their best performance. But most people don’t realize how important tires are to this process – nor how much work it can be keeping tabs on each one in your fleet!
But when every technician today is working with mobile devices as part of their daily work, scanning technology can bring huge efficiencies to this difficult task. By digitizing tire tracking, fleet managers reap the benefits of better performance, lower costs and most importantly, safer customers.