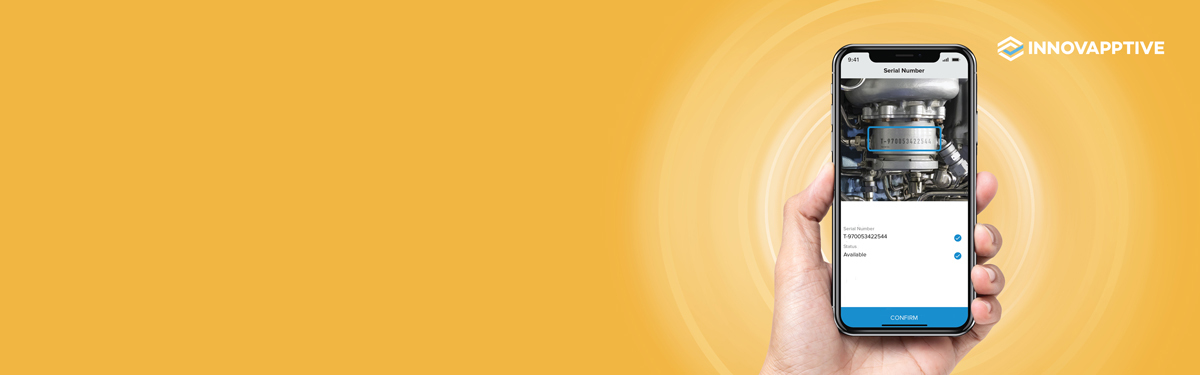
5 Problems Keeping Plant Managers Awake and How a Connected Worker Platform Can Solve Them
By Sundeep Ravande, CEO and co-founder of Innovapptive, Inc.
Modern plant managers have a tough job. Every day they’re responsible for hundreds of lives, and multi-million dollar facilities full of complex equipment and assets. Plant managers must get both to work seamlessly together to turn out a product on time, on budget to drive revenues and build shareholder value.
It’s a job fraught with worry. After all, there’s a lot riding on their shoulders. So it shouldn’t be surprising there are things that keep plant managers awake at night – problems that require more than counting sheep to put their minds at ease.
Today we’re going to look at five of the most pressing of these issues. We’re also going to identify a way to overcome such challenges as well as introduce a partner of Anyline’s you may want to consider if you find your plant facing one or more of these problems.
What are these five sleep-stealing concerns?
1. Employee Health & Safety
Coronavirus infections have shown an unfortunate resurgence in recent weeks after states and cities began reopening their economies and relaxing lockdowns and restrictions after Memorial Day. Keeping front-line workers safe as operations restart is likely the top thing that keeps plant managers up at night. After all, with no workers, there’s no production, and no revenues.
2. Regulatory Compliance
Governments at every level – federal, state, county and city – are increasing environmental, health and safety (EHS) regulations. This is due in part to COVID-19 and the need to safeguard workers from infection. It’s also a result of the growing desire to protect the planet and industrial plant neighbors from harm. Keeping track of these changes is tough enough. Ensuring compliance with them can be labor-intensive and time- consuming tasks. Failure to comply can lead to costly fines, sanctions and litigation that few plant managers or the companies they work for want to face.
3. Profit Margin Pressures
Front-line workers are performing complex jobs using processes and technologies that have remained relatively unchanged. This hurts
their productivity. Lower productivity correlates to maintenance backlogs and unplanned downtime that negatively impacts revenues. Inventory inaccuracies from outdated processes result in higher carrying costs. Ineffective asset tracking methods drive up taxes and insurance premiums. Productivity problems and data inaccuracies put growing pressure on profit margins. In addition, industries are facing greater demand from customers to deliver higher value or a lower cost.
4. Talent & Tribal Knowledge Challenges
An aging workforce and tight labor market have caused skills and talent gaps. Companies have a harder time
recruiting and retaining workers. The Manufacturing Institute estimates that the skills gap means 2.4 million factory job openings might go unfilled through 2028 – half of all open positions. That’s not the only issue. As Baby Boomers retire, they take an unwritten plant and process knowledge with them. Such tribal or institutional knowledge is irreplaceable.
5. High-Value Data for Informed Decision Making
Industrial and manufacturing plants contain hundreds of millions – even billions – of dollars of complex equipment and assets. They also employ a large number of workers. When something goes wrong at a plant, intuition and past experience are seldom a strong foundation for successful long-term operational decisions. Basing decisions on verifiable facts and accurate, real-time data is a sound strategy that yields positive results over time.
Innovapptive - The Connected Worker Platform for SAP
Anyline has recently partnered with a company that can provide solutions to each of these challenges. Innovapptive, a pioneering digital transformation provider, aims to improve the life of the industrial and manufacturing front-line worker through technology. Innovapptive believes in getting jobs done better, faster and safer by digitizing maintenance, warehouse and asset data on mobile devices, tablets, scanners, smart glasses and watches, drones, etc. This eliminates the cumbersome and inefficient paper processes still in use at many industrial plants. It also boosts the utility of other mobile device applications, such as Anyline’s mobile scanning solutions.
Innovapptive’s Connected Worker Platform leverages Anyline’s OCR capabilities to drive workflow automation without barcodes to rapidly recognize assets, equipment, inventory, purchase orders etc. to deliver superior, automated connected worker experiences to the front-line worker. These digital transformation solutions complement Anyline’s capabilities. One such solution is Innovapptive’s platform, which emphasizes digital communication and real-time collaboration between front-line workers, machines and key plant decision makers via workflow automation to complete the last mile between a front-line worker and back-office systems of record, such as SAP and IBM Maximo.
Innovapptive’s Connected Worker Platform leverages Anyline’s OCR capabilities to deliver automated workflows for the following sample use cases:
- Configurable digital checklists to ensure front-line worker health and safety during the COVID-19 crisis and after
- Risk assessment matrices and inspection forms to ensure EHS compliance is in line with governmental agency regulations and corporate policy
- Real-time maintenance, warehouse and asset management data that give an accurate picture of what’s happening at any given moment
- Guided work instructions and other collaboration tools that enable plants to overcome skills gaps, aid recruitment and retention, and transfer tribal knowledge
- High-value, real-time information – verified in the field, on the floor or in the warehouse – that decision makers can analyze for insight to make knowledgeable operational choices the drive revenues, ease margin pressures and enhance competitiveness.